9 Feb
Asylum Research Quantifies the “Last Axis” in Atomic Force Microscopy
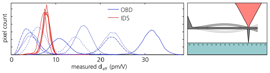
Oxford Instruments Asylum Research announces their development of an interferometric displacement sensor (IDS) that provides a direct measure of AFM cantilever displacement. The IDS interfaces the existing optical system of the Asylum Research Cypher AFM with an external laser Doppler vibrometer. It does not replace the standard laser and detector; rather, it provides a complementary detection method that measures the true tip displacement.
Asylum Research pioneered the introduction of ultra-low noise position sensors as a standard feature on every AFM. Somewhat ironically, though, an equally critical measurement axis, the cantilever displacement, has been neglected. Asylum AFMs and virtually all other commercial AFMs still rely on an indirect measure of cantilever displacement. The optical beam deflection (or “beam bounce”) technique, in which a laser is reflected off the back of the AFM cantilever and on to a position-sensitive detector, is relatively easy to implement and impressively low noise across a wide dynamic range. However, it is fundamentally proportional to changes in the angle of the cantilever and is therefore only indirectly related to the tip displacement. While this measurement technique works remarkably well for some AFM imaging modes, in others, such as piezoresponse force microscopy (PFM), it is known to contribute to significant errors in quantitative analysis.
“Asylum Research was founded on the principle that through careful design, atomic force microscopy can be subject to fewer artifacts and give more quantitative results,” said Asylum Research president Dr. Roger Proksch. “One of Asylum’s core technical strengths is in supporting the fields of piezoelectric and ferroelectric materials research. We’re therefore especially proud to be reinforcing this capability, giving our customers a new and exciting path to more accurate electromechanical measurements. However, we believe the IDS option will also prove useful in characterizing and advancing techniques for nanomechanics, as well as improving our fundamental understanding of the capabilities and possibilities of AFM.”
The module does not interfere with the normal functions of the AFM; it can therefore be used as a secondary channel of information during regular AFM measurements, or it can replace the existing OBD channel for any dynamic imaging mode. A data sheet that further explains the theory, operation, and benefits can be downloaded here.
Figure caption: Histograms of the piezoelectric sensitivity, deff, for five different cantilevers measured with OBD and with IDS. Electrostatic forces between the sample and the body of the cantilever cause the cantilever to oscillate. The resulting changes in the cantilever slope are faithfully reported by the OBD, overwhelming the true electromechanical response of the sample.